W budynkach mieszkalnych coraz częściej instaluje się systemy automatyki sterujące pracą poszczególnych urządzeń i grup urządzeń w celu uzyskania określonych w danym momencie parametrów i stanów. Dodatkowo użytkownik chce mieć również bieżącą informację dotyczącą stanu obiektu. W artykule zostanie przedstawiona koncepcja budowy układu realizującego funkcje systemu sygnalizacji włamania i napadu (SSWiN) oraz systemu sygnalizacji pożarowej (SSP) wykorzystującego sterownik programowalny PLC zamiast standardowej centrali alarmowej. W artykule zostaną przedstawione możliwości i ograniczenia takiego układu w porównaniu z klasycznym wykonaniem systemu SSWiN i SSP.
Wstęp
Od nowoczesnych instalacji elektrycznych stosowanych w budynkach mieszkalnych coraz częściej wymaga się realizacji założeń idei inteligentnych budynków. Jako budynek inteligentny rozumiemy budynek, w którym zainstalowane urządzenia w celowy i właściwy sposób reagują samoistnie na występujące w jego otoczeniu zdarzenia oraz zmieniające się czynniki zewnętrzne [5]. Z punktu widzenia użytkownika budynku mieszkalnego oprócz niezawodności i skuteczności takiego systemu ważne jest jeszcze kilka innych czynników. Pierwszym czynnikiem, szczególnie ważnym na etapie procesu inwestycyjnego, jest ograniczenie kosztów instalacji. Następne cechy, szczególnie ważne już w okresie użytkowania obiektu, to programowalność systemu oraz jego ergonomiczność i energochłonność. Pogodzenie wszystkich przedstawionych cech wydaje się być zrealizowane tylko w przypadku zastosowania systemu zintegrowanego, w którym rolę centrali nadzorująco-sterującej będzie realizował jeden układ, np. sterownik PLC. Takie rozwiązanie upraszcza konfigurację systemu i eliminuje konieczność powielania elementów, które realizują tę samą funkcję, ale współpracują tylko z jednym układem autonomicznym (na przykład tylko z systemem SSWiN). Z drugiej strony uniemożliwia ono jednak wykorzystanie klasycznych układów spełniających wprawdzie tylko wąski, ale wyspecjalizowany zakres możliwości.
W dalszej części artykułu zostanie przedstawiona koncepcja budowy systemów SSWiN i SSP realizowana na bazie sterownika PLC. W opisywanym systemie jako elementy detekcyjne i wykonawcze będą zastosowane standardowe elementy wykorzystywane w klasycznych systemach SSWiN i SSP (detektory, czujki, manipulatory, sygnalizatory optyczno-akustyczne). Niniejszy artykuł odnosi się w szczególności do układów stosowanych w budownictwie (zastosowanie w pojedynczych mieszkaniach lub domach jednorodzinnych, gdzie nie występuje żaden wyspecjalizowany dozór zewnętrzny), dlatego zbudowany system realizujący funkcje SSWiN i SSP będzie musiał spełniać następujące wymagania dotyczące [1]:
- kategorii zagrożenia mienia i osób – Z1 (mienie o małej wartości),
- klasy systemu alarmowego – SA1 i SA2 (zastosowanie w obiektach o małym lub średnim ryzyku szkód),
- klasyfikacji środowiskowej elementów SSWiN – k lasa I i II (wewnętrzna ograniczona i wewnętrzna).
Zaproponowane rozwiązanie ma na celu podniesienie bezpieczeństwa użytkowania całego budynku dzięki zastosowaniu indywidualnych systemów autonomicznych, które w mieszkaniach lub domach jednorodzinnych będą realizować zadania stawiane systemom SSWiN i SSP. Taki system umożliwi również użytkownikowi dostosowanie procedur do własnych potrzeb, szczególnie gdy system realizujący funkcje systemów SSWiN i SSP będzie częścią zintegrowanego systemu sterowania. Dodatkowo celem takiego rozwiązania jest ograniczenie kosztów obsługi tego systemu oraz zewnętrznej ingerencji w pracę systemu, jakie mogłyby zaistnieć w przypadku zastosowania scentralizowanego rozwiązania dla grupy użytkowników. Na stworzonym modelu systemu alarmowego (wykorzystanie modułu MFD firmy Moeller) zostaną przeprowadzone badania sprawdzające możliwości takiego układu w porównaniu z funkcjami i zadaniami realizowanymi przez fabryczne układy decyzyjne (centrale alarmowe) dla systemów SSP i SSWiN spełniające opisane wyżej wymagania.
Sterowniki PLC
Norma IEC 61131-1 [2] definiuje programowalny sterownik cyfrowy (ang. Programmable Logic Controller – PLC) jako cyfrowy system elektroniczny do stosowania w środowisku przemysłowym. Posługuje się on programowalną pamięcią do przechowywania zorientowanych na użytkownika instrukcji w celu sterowania szeroką gamą maszyn i procesów za pomocą cyfrowych lub analogowych wejść i wyjść. Definicja zawarta w normie sugeruje, że sterowniki PLC wywodzą się z automatyki przemysłowej, gdzie były i nadal są wykorzystywane do sterowania grupami urządzeń w procesach produkcyjnych. Bardziej uogólniona definicja sterownika PLC określa go jako układ mikroprocesorowy przeznaczony do sterowania pracą urządzeń i procesów. Sterowniki te spełniają wszystkie funkcje stycznikowych i przekaźnikowych układów sterowania, układów logicznych, programatorów oraz układów przetwarzających sygnały dyskretne i ciągłe [3].
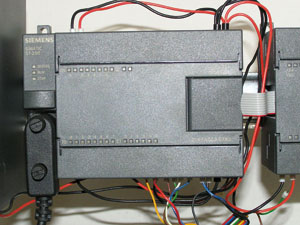
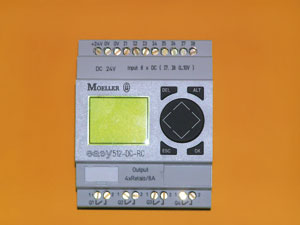
Od czasu pierwszych zastosowań w przemyśle sterowniki PLC przeszły długą drogę w procesie ciągłego dostosowywania się do potrzeb użytkownika. Szybko się okazało, że zalety przemysłowych sterowników PLC zostały zauważone również przez użytkowników ogólnych. Obecnie wyróżnia się dwie grupy sterowników:
- sterowniki przemysłowe (np. Siemens typ S7200; fot. 1a),
- sterowniki do zastosowań ogólnych (np. Siemens LOGO, Moeller Easy; fot. 1b).
Sterowniki przemysłowe z racji przewidzianego zastosowania są bardziej rozbudowane, mają większe możliwości konfiguracyjne, obsługują większą ilość układów wejścia/wyjścia (wejście/wyjście to w skrócie I/O). Jednak są one dość drogie (koszt kilkanaście razy większy w porównaniu z ceną sterownika PLC ogólnego przeznaczenia). Zatem takie układy mogą być wykorzystywane tylko w rozbudowanych systemach automatyki i z racji swojej ceny nie są stosowane ani spotykane w budynkach mieszkalnych. Sterowniki do zastosowań ogólnych są układami mniej skomplikowanymi pod względem technologicznym, dzięki czemu ich cena jest dużo niższa (koszt pojedynczego sterownika kształtuje się już od kilkuset złotych). Ich możliwości programowe nie odbiegają od możliwości sterowników przemysłowych (ograniczona jest jedynie liczba poszczególnych modułów funkcyjnych i układów I/O). Obecnie pewnym standardem stało się wyposażanie sterowników PLC we wbudowane układy komunikacyjne, umożliwiające zarówno ich łączenie z jednostką programującą (port komunikacyjny sterownika-komputer), jak i ich wzajemną współpracę. Takie rozwiązanie umożliwia budowę rozproszonych systemów sterujących, które zwiększają możliwości konfiguracyjne systemu przy jednoczesnym ograniczeniu okablowania instalacyjnego.
Uruchomienie sterownika PLC rozpoczyna się od wpisania algorytmu programu do jego pamięci operacyjnej. W tym celu można wykorzystać wbudowane w sterownik przyciski funkcyjne. Najczęściej jednak wczytanie programu odbywa się z komputera PC z zainstalowanym programem konfiguracyjnym za pomocą przewodu komunikacyjnego.
Zgodnie z normą IEC 61131 [2] określone zostały następujące ujednolicone języki programowania:
- języki tekstowe:
• IL (Instruction List) – listy instrukcji,
• ST (Structured Text) – tekst strukturalny.
- języki graficzne:
• LD (Ladder Diagram) – schemat drabinkowy,
• FBD (Function Blok Diagram) – schemat bloków funkcyjnych,
• grafy sekwencji SFC (Sequential Function Chart).
Ze względu na realizowane zadania w sterowniku PLC wyróżnia się trzy podstawowe elementy [4]:
- moduły wejściowe, których zadaniem jest wprowadzanie do systemu sterownika analogowych i cyfrowych sygnałów wejściowych (np. z czujek, łączników);
- jednostkę centralną (CPU), która przetwarza sygnały wejściowe zgodnie z zadanym (zapisanym w pamięci sterownika) algorytmem oraz przekazuje wyniki na wyjścia;
- moduły wyjściowe, których zadaniem jest przekazywanie obliczonych wartości do elementów wykonawczych.
Zadaniem sterownika programowalnego jest sterowanie wyjściami na podstawie informacji otrzymywanych z wejść sterownika oraz procedur zawartych w blokach funkcyjnych.
System SSWiN i SSP oparty na sterowniku PLC jako jednostce zarządzającej
Zadanie stawiane systemom alarmowym to skuteczne powiadomienie użytkownika o zaistniałym zagrożeniu. Technicznie jest to zespół współpracujących urządzeń (również z instalacją przewodową), które mają na celu wykrywanie zagrożeń, wywołanie alarmu oraz inicjowanie przedsięwzięć zmierzających do likwidacji takiego zagrożenia. Ze względu na cele stawiane takiemu systemowi można w nim wyodrębnić kilka podstawowych powiązanych ze sobą bloków funkcyjnych (rys. 1):
- blok analizująco-decyzyjny,
- blok detekcyjny (wejściowy),
- blok alarmująco-informujący (wykonawczy),
- blok zasilający układ.
W zależności od przyczyny wywołania alarmu (w przypadku systemu SSWiN jest to naruszenie strefy chronionej, a w przypadku systemu SSP – wykrycie ogniska pożaru) rola systemu nadzorującego wykorzystywanego w obiektach mieszkalnych (mieszkania lub domy jednorodzinne) sprowadza się zazwyczaj do powiadomienia użytkownika oraz otoczenia o zaistniałym zagrożeniu. Dodatkowo, jeśli spełnione są pewne konieczne wymagania techniczne (np. powiązanie systemu SSWiN lub SSP z innymi systemami automatyki budynku), może również nastąpić dalsze przekazanie informacji do innych układów, które spowodują na przykład blokadę wyjść (w przypadku wykrycia włamania) lub odbezpieczenie zamków wyjść (w przypadku wykrycia zagrożenia pożarowego).
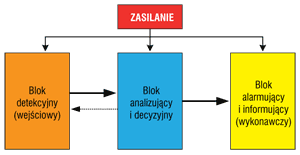
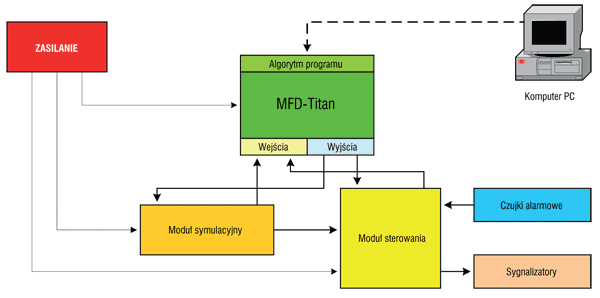
Na rys. 2 przedstawiono schemat blokowy systemu realizującego funkcje systemów SSWiN i SSP oraz wykorzystującego sterownik PLC jako jednostkę sterującą pracą układu.
Na rys. 2 oprócz sterownika PLC, elementów detekcyjnych i sygnalizacyjnych, które wchodzą w skład tradycyjnego schematu blokowego systemu alarmowego, umieszczono także blok symulacyjny i blok sterowania (pośredniczący). Za pomocą tych bloków możliwe jest podłączenie poszczególnych manipulatorów, czujek alarmowych i sygnalizatorów oraz przeprowadzenie symulacji działania zaproponowanego algorytmu bez konieczności podłączania do wejść i wyjść rzeczywistych elementów.
Taka budowa stanowiska umożliwia przeprowadzenie pełnej symulacji oraz zaprezentowanie możliwości i funkcjonalności poszczególnych elementów systemu alarmowego. Za pomocą odpowiedniej konfiguracji modelu możliwe jest również badanie fabrycznych central alarmowych.
Do badań użyto sterownika MFD-Titan firmy Moeller (fot. 2) jako układu realizującego funkcję centrali alarmowej. W jego skład wchodzą następujące podzespoły:
- moduł CPU – MFD-CP8-NT,
- moduł wyświetlacza – MFD-80-B,
- moduł wejść/wyjść – MFD-R16.
Na fot. 3 został przedstawiony widok panelu czołowego modelu systemu alarmowego, który wykorzystuje sterownik PLC jako centrum decyzyjne.

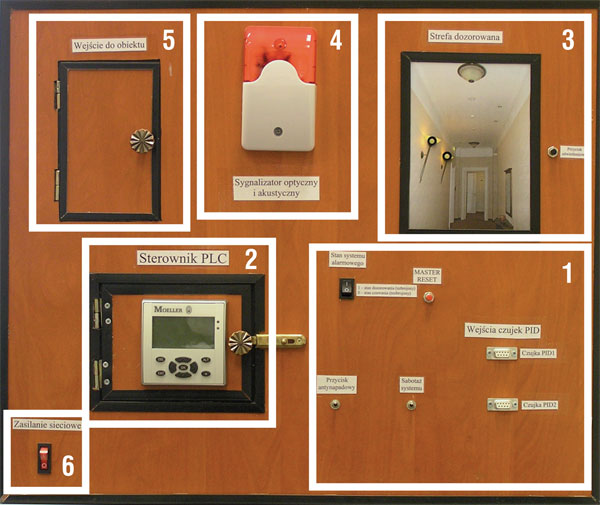
MFD-Titan, 3 – panel oświetleniowy, 4 – sygnalizator optyczno-akustyczny, 5 – panel symulujący wejście do obiektu,
6 – włącznik/wyłącznik zasilający sterownik PLC oraz elementy i urządzenia z panelu przedniego z wykorzystaniem sterownika PLC
Umieszczony na płycie czołowej panel symulacyjny i wejściowy (obszar 1 na fot. 3) umożliwia zarówno zasymulowanie pewnych zdarzeń, jak i podłączenie rzeczywistych obiektów w celu sprawdzenia działania takiego systemu w rzeczywistości. W charakterze elementów wejściowych można podłączyć szeroką gamę czujek alarmowych stosowanych w systemach SSWiN (czujki PIR, mikrofalowe, mikrofonowe, kontaktronowe) oraz systemach SSP (optyczne lub jonizacyjne czujki dymu), manipulatorów i zamków szyfrowych. Na fot. 4 przedstawiono elementy współpracujące z klasycznymi (fabrycznymi) centralami alarmowymi, wykorzystanymi do współpracy ze sterownikiem PLC, które tworzą alternatywne do fabrycznych rozwiązanie budowy systemu SSWiN i SSP. Dodatkowo pod poszczególne wyjścia sterownika można podłączać inne urządzenia elektryczne niespełniające wprawdzie w systemie zadań związanych z realizacją funkcji systemów SSWiN i SSP, ale mogące z nimi w spółpracować. Przykładem takiej współpracy może być wykorzystanie jako czujki obecności czujek PIR do załączania w pomieszczeniach oświetlenia elektrycznego (wyjście Q1) w systemie wyłączonym ze stanu dozoru.
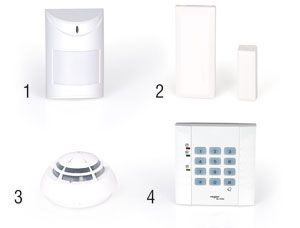
podczerwieni typu Satel Aqua, 2 – czujka kontaktronowa,
3 – optyczna czujka dymu typu ADR-20N, 4 – zamek typu
Roger SL1000
Wyniki badań testowych
Możliwości tak stworzonego układu zostały sprawdzone na kilku hipotetycznych, ale możliwych do wystąpienia w rze-czywistości projektach. Jednym z przykładów wykorzystania modelu jest układ sterowania systemem alarmowym wykorzystującym osiem wejść, cztery wyjścia cyfrowe oraz dwie diody wbudowane w panel sterownika.
Założenia do projektu są następujące:
- Czujka PIR 1 (I1) zasilana jest na stałe ze źródła niezależnego od pracy sterownika PLC; wejście w obszar jej działania wtedy, gdy system nie jest włączony w dozór spowoduje zgaszenie/zapalenie oświetlenia na korytarzu, a w stanie dozorowania po czasie t = 8 s powoduje wywołanie optyczno-akustycznego sygnału alarmowego (Q2) oraz zapalenie oświetlenia na korytarzu (Q3).
- Czujka PIR 2 (I2) początkowo jest nieaktywna; jej zasilanie jest załączane po czasie t = 31 s od przejścia w stan dozorowania; jej aktywacja w tym stanie powoduje wywołanie optyczno-akustycznego sygnału alarmowego oraz zapalenie oświetlenia na korytarzu.
- Naruszenie linii sabotażowej czujek PIR 1 lub PIR 2 (I3) w stanie wyłączenia z dozoru powoduje wywołanie akustycznego sygnału alarmowego oraz miganie czerwonej diody na panelu sterownika (LE2), a w stanie dozorowania powoduje wywołanie optyczno-akustycznego sygnału alarmowego, zapalenie oświetlenia na korytarzu oraz wyświetlenie komunikatu „sabotaż!”.
- Załączanie w dozór/wyłączanie z dozoru odbywa się za pomocą przełącznika podłączonego do wejścia sterownika (I5).
- Załączenie/wyłączenie oświetlenia na korytarzu odbywa się za pomocą przycisku podłączonego do wejścia sterownika (I6).
- Otwarcie drzwi powoduje rozwarcie styków kontaktronu, zamknięcie – zwarcie styków.
- Kasowanie zawartości komórek pamięci: markerów M, wyjść sterownika Q (przejście w stan niski – 0V).
Podanie napięcia na poszczególne wejścia sterownika (stan wysoki – 24 V) odpowiada za:
- I1 – zadziałanie pasywnej czujki podczerwieni PIR 1,
- I2 – zadziałanie pasywnej czujki podczerwieni PIR 2,
- I3 – wysłanie sygnału sabotażowego z czujek PIR 1 lub PIR 2,
- I4 – wywołanie alarmu napadowego,
- I5 – uzbrojenie/rozbrojenie alarmu za pomocą manipulatora,
- I6 – zapalenie/zgaszenie diod LED,
- I9 – zadziałanie kontaktronu zamontowanego w drzwiach,
- I10 – centralny reset sterownika PLC (kasowanie zawartości: M, Q).
Wyjścia sterownika odpowiadają za załączenie:
- Q1 – sygnału akustycznego,
- Q2 – sygnału optyczno-akustycznego,
- Q3 – zapalenia diod LED (oświetlenie korytarza),
- Q4 – źródła zasilania czujki PIR 2,
- LE1 – zapalenie/zgaszenie oświetlenia wyświetlacza sterownika,
- LE2, LE3 – zapalenie/zgaszenie diod na panelu sterownika (odpowiednio: czerwona, zielona).
Na rys. 3 został zaprezentowany algorytm pracy systemu alarmowego działającego i realizującego założenia projektowe opisywanej konfiguracji. Natomiast na rys. 4 przedstawiony został fragment schematu drabinkowego algorytmu sterującego pracą systemu.
Podsumowanie
Po dokonaniu serii badań testowych na stworzonych algorytmach sterujących oraz później na systemach zbudowanych z rzeczywistych elementów należy stwierdzić, że tak zbudowane systemy spełniają swoją rolę i mogą być przeznaczone do ochrony obiektów o małym lub średnim ryzyku szkód (systemy klasy SA1 i SA2), a także do ochrony mienia o małej wartości (kategoria Z1).
Współpraca elementów klasycznego systemu alarmowego ze sterownikiem programowalnym jest na ogół bezproblemowa. Zwrócić należy jedynie uwagę na staranny dobór wartości napięć znamionowych elementów wejściowych i wyjściowych, dzięki czemu czujki i sygnalizatory zastosowane w systemie alarmowym (zbudowanym na przykład z wykorzystaniem centrali alarmowej CA6 firmy Satel) spełniają te same funkcje co w przypadku zastosowania sterownika programowalnego MFD-Titan firmy Moeller. W przypadku różnych wartości napięć znamionowych istnieje konieczność wyposażenia systemu w układy dopasowujące (np. układy przekaźnikowe lub dzielniki napięć).
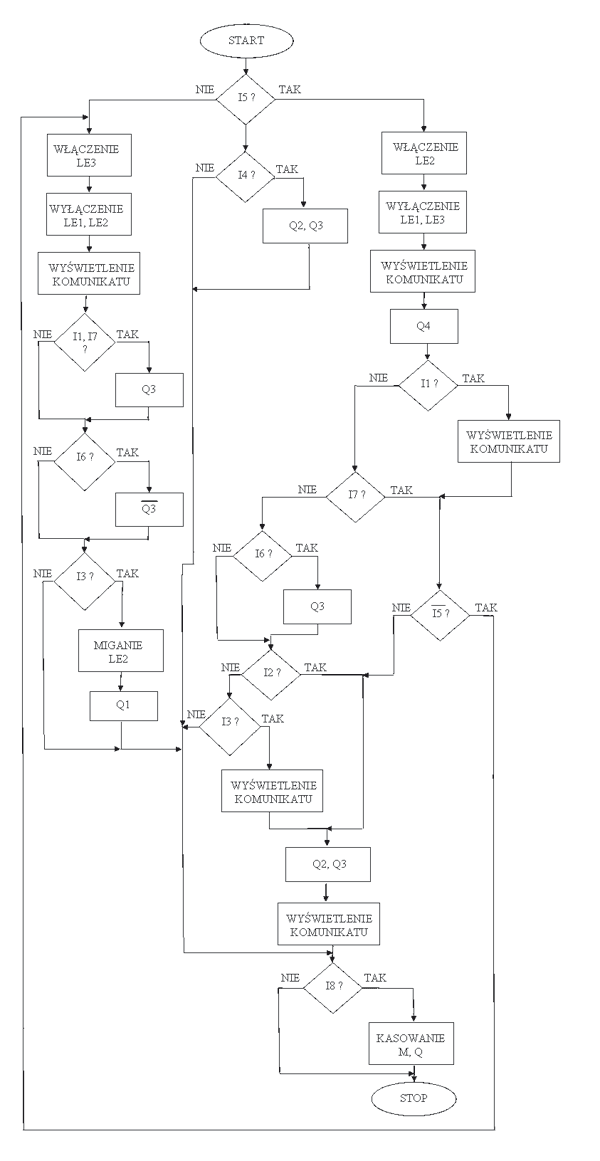
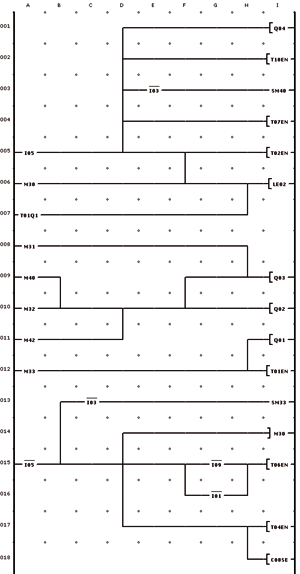
W odróżnieniu od rozwiązań fabrycznych system zbudowany na bazie sterownika PLC ma możliwość dowolnego kształtowania algorytmu sterującego. Szczególnie ważne jest to w przypadku wykorzystania takich układów w mieszkaniach lub budynkach mieszkalnych. Daje to użytkownikowi możliwość doboru indywidualnych parametrów i indywidualnej konfiguracji sprzętowej. Wadą tego rozwiązania jest natomiast konieczność poznania przez użytkownika co najmniej jednego języka programowania sterowników PLC.
Dzięki modułowej budowie tych układów istnieje możliwość szybkiej rozbudowy systemu, co jest ważną zaletą. A poprzez zastosowanie dodatkowych elementów (np. układów I/O) system może mieć charakter systemu rozproszonego.
dr inż. Marcin Buczaj
mgr inż. Piotr Kowalik
Politechnika Lubelska
Katedra Inżynierii Komputerowej i Elektrycznej
Literatura
- PN-EN 50131-1:2002 Systemy alarmowe – Systemy sygnalizacji włamania – Część 1: Wymagania ogólne.
- Norma PN-EN 61131 – Sterowniki Programowalne.
- Brock S., Muszyński R., Urbański K., Zawirski K.: Sterowniki programowalne. Wydawnictwo Politechniki Poznańskiej, Poznań 2000.
- Kasprzyk J.: Programowanie sterowników przemysłowych. Wydawnictwo Naukowo-Techniczne, Warszawa 2006.
- Petykiewicz P.: Nowoczesna instalacja elektryczna w inteligentnym budynku. COSiW SEP, Warszawa 2001.
- www.automatyka.siemens.pl
- www.moeller.pl
Zabezpieczenia 3/2009